Answer:
475.14 psi
Step-by-step explanation:
Given:-
- The steel bolts standard used = W 7/16''
- The number of bolts for the flange , n = 4
- The pitch of each bolt, k = 1 / 16 inch / turns
- The diameter of flange end-plate, D = 16''
- The length of useful length of bolt, L_b = 16''
- The thickness of vessel's walls , t = 0.125''
- The additional amount of turn after snug fit, T = 1/2
Find:-
Production of pressure vessels is fastening an open-ended cylinder and two rigid plates with bolts. Calculate the pressure that the container will start to leak.
Solution:-
- The end-plates ( Flanges ) experience a constant force ( F ) due to pressure "p" of the pressurized gas in the vessel.
- The force experienced due to pressure "p" by each of the end-plates can be determined from the following relation:

Where,
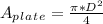
Hence,

- Each end plate is fitted with n = 4 identical bolts ( W 7/16'' ). The tensile force experienced by each bolt ( Fb ) fastened into the end-plate is:

- The amount of stretch ( deformation ) in each bolt ( δb ) can be represented by Young's modulus ( E ) expression for the bolts.
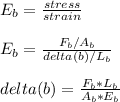
Where,
δb = delta ( b ) : The deformation in each bolt ( stretch )
E_b = Elastic modulus ( steel ) - (ASTM A-36) = 30 Mpsi
d_b = Diameter of bolt used = 5 / 8 '' ( W 7 / 16'' )
A_b =

- Care must be taken when visualizing the strains in the end caps as it is subjected to poisson contraction.
- The increase in pressure "p" will induce hoop stress and consequently hoop strain. ( Radial expansion )
- According to material law, an expansion in one dimension leads to a contraction in the other dimension such that the volume of material ( pressure vessel ) used remains constant.
- Therefore, we expect to see a "poisson contraction" of the axial length of the pressure vessel.
- This advertently leads to a small clearance " c " between the end plates and the ends of the pressure vessel circumferential thickness. This very clearance becomes a source of leakage from flanged ends of the pressure vessels.
- We need to determine the minimum clearance " c " required for the leakage to occur.
- The flange bolts are tightened with "T" turns after snug fitting. These turns made chiefly using a wrench provides the requisite axial preloading of the flange end-plates against pressure vessel ends.
- The axial length through which the bolts are turned are identical for all bolts. They are mathematically expressed as:
Turned length = T*k
- For the leakage to occur the amount of axial contraction must be at-least the amount of clearance i.e turned length. Hence, the clearance is:
c = Turned length = T*k
- The axial contraction ( longitudinal deformation ) of the pressure vessel ( δc ) is simply the product of strain in the axial direction ( εa ) and length of the bolt ( L_b )

Where,
delta ( c ) = δc ... longitudinal deformation
strain ( a ) = εa ... longitudinal strain.
- Use the appropriate stress-strain relationship for longitudinal strain ( εa ) considering the poisson ratio ( ν ).
εa =

Where,
stress ( a ) = longitudinal stress = 0
( Leakage: the stress in axial direction has vanished )
stress ( h ) = Hoop stress
E_c : Modulus of elasticity of pressure vessel ( Brass )
E_c = 16.3 Mpsi , ν = 0.344
- The hoop stresses are defined as:
σh =

- The strain in axial direction ( εa ) would be:
εa =

- The axial deformation in the cylinder ( δc ) becomes:
δc =

- So, the net deformation ( δ_net ) is due to the elongation of each bolts ( δb = delta ( b ) ) and contraction of cylinder ends for the amount of axial deformation ( δc = delta ( c ) ).
δ_net = δb + δc = c = T*k
- The relation becomes:
![(F_b*L_b)/(A_b*E_b) - ( v*p*D*L_b )/(2*t*E_c) = T*k\\\\p* [ (4*\pi *D^2*L_b)/(16*\pi*d_b^2 *E_b) - ( v*D*L_b )/(2*t*E_c) ] = T*k\\\\p* [ (\pi *D^2*L_b)/(4*\pi*d_b^2 *E_b) - ( v*D*L_b )/(2*t*E_c) ] = T*k\\\\](https://img.qammunity.org/2021/formulas/engineering/college/snz6q6vw77v2rplxf2y44edr8fpqx6xe6x.png)
- Now we can solve for the maximum pressure "p" allowable to prevent leakage:
![p* [ (16^2*16)/(4*(5/8)^2 *30) - ( 0.344*16*16 )/(2*0.125*16.3) ] = (1)/(2) *(1)/(16) *10^6\\\\p* [ 87.38133 - 21.61079 ] = 31250\\\\p = (31250)/(65.77054)\\\\p = 475.14 psi](https://img.qammunity.org/2021/formulas/engineering/college/e2bs2c0haklegenne2saguhkh3oe8ebldz.png)
Answer: The pressure at which the cylinder will start to leak would be 475.14 psi.