Answer:
The radius of the specimen is assumed to be 9.724 mm
Step-by-step explanation:
Given that:
For a cylindrical specimen of a brass alloy;
The length = 104 mm, Elongation = 5.20 mm and the tensile load = 101000 N
Let's first determine the radius of the cylindrical brass alloy from the knowledge of the cross-sectional area of a cylinder.




To estimate the tensile stress:
We need to first determine the strain relating to elongation at 5.20 mm
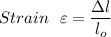
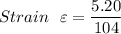
Strain ε = 0.05
Using the stress-strain plot; let assume that under the circumstances;
= 340 MPa for stress corresponding to 0.05 strain
Thus;
The cylindrical brass alloy radius

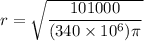
r = 0.009724 m
r = 9.724 mm