Answer:
Among all three tools, the ceramic tool is taking the least time for the production of a batch, however, machining from the HSS tool is taking the highest time.
Step-by-step explanation:
The optimum cutting speed for the minimum cost
![V_(opt)= (C)/(\left[\left(T_c+(C_e)/(C_m)\right)\left((1)/(n)-1\right)\right]^n)\;\cdots(i)](https://img.qammunity.org/2021/formulas/engineering/college/1qev1ldj8c2vmtgviit3uuk9qc3mwtliiw.png)
Where,
C,n = Taylor equation parameters
=Tool changing time in minutes
=Cost per grinding per edge
= Machine and operator cost per minute
On comparing with the Taylor equation
,
Tool life,
![T= \left[ \left(T_t+(C_e)/(C_m)\right)\left((1)/(n)-1\right)\right]}\;\cdots(ii)](https://img.qammunity.org/2021/formulas/engineering/college/z5ed4wcwqwpq2mqfsnx9k7xph36t5ocxiu.png)
Given that,
Cost of operator and machine time

Batch setting time = 2 hr
Part handling time:
min
Part diameter:

Part length:

Feed:

Depth of cut:

For the HSS tool:
Tool cost is $20 and it can be ground and reground 15 times and the grinding= $2/grind.
So,

Tool changing time,
min.


(a) From equation (i), cutting speed for the minimum cost:
![V_(opt)= \frac {80}{\left[ \left(3+(3.33)/(0.667)\right)\left((1)/(0.13)-1\right)\right]^(0.13)}](https://img.qammunity.org/2021/formulas/engineering/college/kfmbmufuh7rd4n39b48jq0fr2evlcax2gj.png)
m/min
(b) From equation (ii), the tool life,
![T=\left(3+(3.33)/(0.667)\right)\left((1)/(0.13)-1\right)\right]}](https://img.qammunity.org/2021/formulas/engineering/college/uw232a8jig9s943panl4hai5smmijvcjq2.png)
min
(c) Cycle time:

where,
Machining time for one part
Number of pieces cut in one tool life
min, where
is the rpm of the spindle.
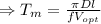

So, the number of parts produced in one tool life


Round it to the lower integer

So, the cycle time
min/pc
(d) Cost per production unit:
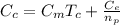

(e) Total time to complete the batch= Sum of setup time and production time for one batch
.
(f) The proportion of time spent actually cutting metal

Now, for the cemented carbide tool:
Cost per edge,

Tool changing time,



(a) Cutting speed for the minimum cost:
[from(i)]
(b) Tool life,
[from(ii)]
(c) Cycle time:



[ nearest lower integer]
So, the cycle time

(d) Cost per production unit:
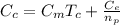

(e) Total time to complete the batch
.
(f) The proportion of time spent actually cutting metal

Similarly, for the ceramic tool:



(a) Cutting speed:
![V_(opt)= \frac {3500}{\left[ \left(1+(1.67)/(0.667)\right)\left((1)/(0.6)-1\right)\right]^(0.6)}](https://img.qammunity.org/2021/formulas/engineering/college/bgyqu6wc4hie67lqgwjee8h6vpabz192po.png)

(b) Tool life,
![T=\left[ \left(1+(1.67)/(0.667)\right)\left((1)/(0.6)-1\right)\right]=2.33 min](https://img.qammunity.org/2021/formulas/engineering/college/ji5bwmd61g5hsh4dte7ac9ajs26k8givlg.png)
(c) Cycle time:




So,

(d) Cost per production unit:
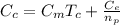

(e) Total time to complete the batch
.
(f) The proportion of time spent actually cutting metal
