Answer:
EOQ 149 units
ROP 160 units
average inventory 80 units
holding cost $720
orders per year 25
ordering cost $625
Step-by-step explanation:
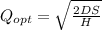
D = annual demand 4,000
S= setup cost = ordering cost 25
H= Holding Cost 9.00
EOQ = 149
lead time: 2 weeks
ROP: annual demand x lead time/year
ROP: 80 units per week x 2 = 160
As the ROP is greater than EOQ the company's inventory will be his ROP
meaning it will order as soon as a new order arrives.
average inventory ROP/2 = 160/ 2 = 80
annual holding cost: 80 units on average x 9 dollars each = 720
order per year: 4.000 / 160 = 25
total ordering cost: 25 orders x 25 dollars each: 625